Die Kartonagen werden nach dem Wareneingang semiautomatisch und die Mehrweg-Kisten automatisch depalettiert und in einen Bahnensorter als Zwischenpuffer artikelrein in Durchlaufbahnen transportiert. Nach dem Eingang der Marktbestellung werden mittels eines Packmustergenerators die Mischpaletten berechnet und für die Kommissionierung freigegeben. Im Anschluss transportiert das System die Kisten und Kartons entsprechend der Reihenfolge aus dem Zwischenpuffer zu den semiautomatischen Kommissionierarbeitsplätzen.
„Mit dem Flowpicker treten wir den Herausforderungen bei der manuellen Kommissionierung, insbesondere in der Obst- und Gemüseabteilung, entgegen“, sagt Ricco Cerniglia, Bereichsvorstand Supply Chain Management bei Kaufland. Für die Mehrweg-reinen Mischpaletten werden die Kisten aus dem Zwischenpuffer zu den automatischen Palettierrobotern transportiert. Nachdem die Mischpaletten gebildet sind, werden diese automatisch zu den Bereitstellbahnen und von dort manuell direkt an die Verladetore transportiert.
Das neue System unterstützt Mitarbeiterinnen und Mitarbeiter ergonomisch.
Martin Gräb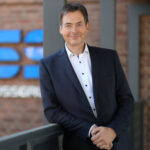
Für die Kartonkommissionierung arbeitet das System nach dem Prinzip ‘Ware zur Person’ und nutzt Ziehen und Schieben statt Heben, um die Kisten zu bewegen. „Das entlastet die Mitarbeiter enorm.“, sagt Martin Gräb, Geschäftsführer des Projektpartners BSS Bohnenberg.
Das System ist flexibel bei der Verarbeitung von wiederverwendbaren Mehrwegladungsträgern (Faltkisten), die bevorzugt verwendet werden und deren Quote stetig steigt, sowie Einwegkartons. Das trägt zur Effizienz und Praktikabilität bei.
Für das Projekt erhielt Kaufland den reta award 2024 in der Kategorie „Best AI & Robotics“. BSS Bohnenberg wurde als Top Supplier Retail geehrt.