Am alten Standort war Coop Norge an die Kapazitätsgrenze gestoßen. Früher wurden Frischfleisch und Getränke direkt vom Lieferanten an die Filialen geliefert, inzwischen hat Coop die Lieferlogistik dieser Sortimente an die Geschäfte übernommen. In dem erforderlich gewordenen Neubau des Logistikzentrums sah der Händler zugleich die Chance, die Wettbewerbsfähigkeit insgesamt zu verbessern. Denn mit der Umstellung von zuvor rein manuell betriebenen Lager- und Kommissionier-Prozessen auf einen hohen Automatisierungsgrad wurde Coop unabhängiger von der angespannten Arbeitsmarktlage. „Wir haben in Norwegen eine niedrige Arbeitslosenquote sowie ein hohes Lohnniveau“, erklärt Halvor Nassvik, Senior Manager für das Projekt „Coop Logistikzentrum Gardermoen („CLog“).“ Er glaubt überdies, „dass es zukünftig schwierig wird, für die körperlich anstrengenden und meist monotonen Arbeiten junge Leute zu finden.“
Filial-Logistik mit Herausforderungen
Die wirtschaftliche Distribution von Lebensmitteln und Non-Food-Artikeln ist in Norwegen eine Herausforderung. „Das liegt an der niedrigen Bevölkerungszahl und den zahlreichen kleinen Geschäften, die über das ganze Land verteilt sind. Zudem hat Norwegen eine Nord-Süd-Ausdehnung von über 2.000 Kilometern“, so Nassvik. Deshalb müssten jede Palette und jeder LKW optimal mit Waren gefüllt werden. Aufgrund der Entfernungen, die zurückgelegt werden, sind eine fehlerfreie Belieferung und hohe Produktqualität zwingend notwendig.
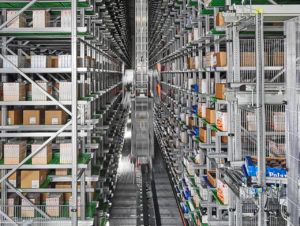
Die 52.000 qm große Anlage beliefert circa 1.200 Filialen mit mehr als 17.000 verschiedenen Artikeln. (Foto: Witron)
Das „CLog“ in unmittelbarer Nähe zum Flughafen Oslo hat in der Logistikstruktur von Coop mehrere Funktionen: Zum einen dient es als Distributionszentrum für die Region, in der Coop Norwegen rund 40 Prozent seines Umsatzes erwirtschaftet. Hier beliefert das Coop Logistikzentrum die Filialen mit Waren aus dem vollen Artikelsortiment: Trockensortiment (+ 18 Grad Celsius), Obst & Gemüse (+ zwölf Grad Celsius /+7 Grad Celsius), Frischesortiment (+ zwei Grad Celsius) und Tiefkühlsortiment (-25 Grad Celsius). Zum anderen fungiert das Logistikzentrum als zentrales Distributionszentrum für Langsam- und Mitteldreher aus dem Trocken- und Frischebereich – und damit als Umschlagspunkt für vier weitere Coop-Regionalläger in Norwegen.
Die 52.000 qm große Anlage, die stufenweise hochgefahren wurde, beliefert circa 1.200 Filialen mit mehr als 17.000 verschiedenen Artikeln. An einem Spitzentag können nach Unternehmensangaben bis zu 480.000 Handelseinheiten kommissioniert werden. Geplant und realisiert wurde das Logistikzentrum vom Generalunternehmer Witron Logistik und Informatik aus Parkstein. Witron ist zudem für den technischen Betrieb der Anlage verantwortlich, ein Team ist stets vor Ort.
Rund 95 Prozent automatisiert
Etwa 95 Prozent aller Artikel werden heute bei Coop automatisiert bzw. teilautomatisiert gelagert und kommissioniert. In sämtlichen Temperaturbereichen kommt das vollautomatische Kommissioniersystem „Order Picking Machinery (OPM)“ zum Einsatz. Es schichtet Handelseinheiten, Behälter, Kartons oder PET-Flaschen komplett ohne Personaleinsatz filialgerecht auf Paletten beziehungsweise Rollcontainer. Das „Dynamic Picking System (DPS)“ zur Kommissionierung von kleinvolumigen Artikeln wird für das Trockensortiment und im Frischebereich genutzt. Die Artikel befinden sich, abhängig von der Auftragsstruktur, permanent beziehungsweise bedarfsgerecht in der Pickfront, die ihrerseits durch Regalbediengeräte automatisiert optimiert wird. Coop kommissioniert im DPS nicht „klassisch“ von Behälter in Behälter, sondern von Behältern direkt in Versandkartons. Grund dafür wären lange Lieferwege, eine Rückführung der Behälter wäre nicht wirtschaftlich. Darüber hinaus werden die via DPS kommissionierten Versandkartons direkt dem OPM-System zugeführt, womit eine Auftragskonsolidierung zwischen den beiden Systemen stattfindet.
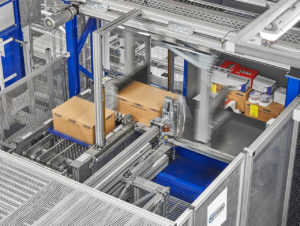
Etwa 95 Prozent aller Artikel werden heute bei Coop automatisiert bzw. teilautomatisiert gelagert und kommissioniert. (Foto: Witron)
Mit Hilfe des „Car Picking System (CPS)“ wird sperrige Ware des Trockensortiments kommissioniert. Es sorge für kurze Fahrwege im Verteilzentrum und eine deutliche Verbesserung der Ergonomie – in Skandinavien gelten diesbezüglich strenge gesetzliche Vorgaben. Das Steuerungssystem ermöglicht, mehrere Aufträge parallel von einem Kommissionierer zu picken. Bei Coop wird mittels Pick-by-Voice von Palette (Mittel- und Schnelldreher) beziehungsweise Layer-Tray (Langsamdreher) auf die Auftragspalette kommissioniert. Diese Technologie wird auch bei Promotion-Artikeln und Display-Paletten angewendet. Von Witron entwickelte, ergonomische Layer-Trays sollen gewährleisten, dass eine Vielzahl weiterer Artikel in der Pickfront platzsparend vorgehalten werden können. Durch den Einsatz der Layer-Trays verringern sich die Kommissionierwege um etwa 60 Prozent, so heißt es.
Warenausgangspuffer reduziert LKW-Ladezeiten
Die Prozesse im Versandbereich optimiert ein automatisierter Warenausgangspuffer. Bei Coop beträgt die Temperatur im Versandbereich konstant + 4 Grad Celsius. „Dadurch sind wir in der Lage, die fertig kommissionierten Aufträge aus den verschiedenen Temperaturzonen zentral zu puffern, touren- und filialbezogen zu konsolidieren und termingerecht zur Auslieferung direkt vor dem richtigen Versandtor bereitzustellen“, erklärt Jack Kuypers, Vice President Witron North West Europe. Coop profitiere u. a. von den dadurch sehr kurzen Laufwegen der Versandmitarbeiter bei der LKW-Beladung. Somit verringert sich die Beladezeit an den Toren und die Fahrzeuge können sich schneller auf den Weg zu den Filialen machen“, so Kuypers.
Neuland betrat Witron bei der Paletten-Identifikation: In Skandinavien werden die Distributionszentren von ihren Lieferanten mit Kunststoffpaletten beliefert, die mit integrierten RFID-Transpondern ausgestattet sind. Zusätzlich kommen Holzpaletten zum Einsatz, welche im Wareneingang automatisch ein RFID-Label erhalten. Beide Paletten-Typen sollten auf Wunsch von Coop auch im automatisierten Logistiksystem flexibel gehandhabt werden können. Die zwei Varianten können nun im gesamten Materialfluss identifiziert und verwaltet werden.
Fotos (3): Witron
Weitere Informationen: www.witron.de